CONVENTIONAL NDT
Deem Inspection provides Industrial Radiography Services in both our laboratory and in the field at Customer locations/Site. Our radiographers are Well experienced in many different speciality Techniques involving geometrically challenged Parts and equipment's.
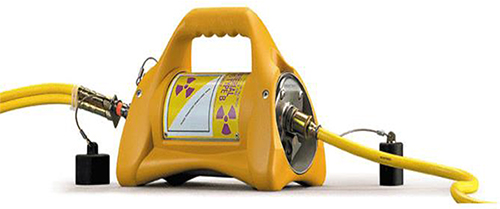
SOURCE : IRIDIUM 192
Our Company is certified by the KACARE (regulatory authority of Atomic Energy in Saudi Arabia ) and is obliged to use the radiographic source with maximum Safety and care upon usage in Site and Safely returned back to the Storage pit after use.
Our Technicians and Safety Officers are all well trained to handle all kinds of situations as SAFETY IS PRIORITY AND SAFETY COMES FIRST.
Ultrasonic Testing (UT) uses high frequency sound energy to conduct examinations and make measurements. Ultras onic inspection can be used for flaw detection/evaluation, dimensional measurements, material characterization, which consists of pulsar/receiver , the transducer generate s high frequency ultrasonic energy. The sound energy is introduced and propagates through the materials in the form of waves. When there is a discontinuity (such as a crack) in the wave path, part of the energy will be reflect ed back from the flaw surface.
PULSE ECHO TECHINIQUE
It is a diagnostic technique in which short-duration ultrasound pulses are
transmitted into the region to be studied, and echo signals resulting from
scattering and reflection are detected and displayed. The depth of a reflecti
ve structure is inferred from the delay between pulse transmission and
echo reception.
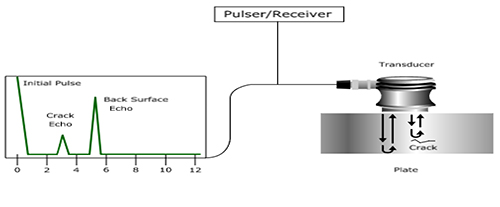
Magnetic Particle Testing (MPT), also referred to as Magnetic Particle Inspection, is a nondestructive examination (NDE) technique used to detect surface and slightly subsurface flaws in most ferromagnetic mat erials such as iron, nickel, and cobalt, and some of their alloys.
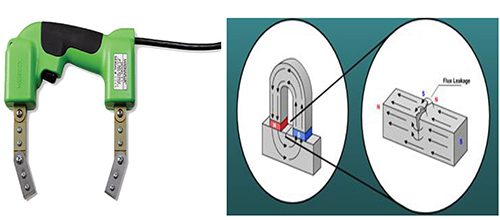
Liquid penetrant inspection is a nondestructive test method which does not harm the samples or parts being inspected. The test is very effective in detecting porosity, cracks , fractures, laps, seams and other flaws that are open to the surface of the test piece a nd may be caused by fatigue, impact, quenching, machining, grinding, forging, bursts, shrinkage or overload. As a result, it is often used on lots of machined parts, manufact ured products, castings, forgings and other items that will be placed into service. Liqui d penetrant inspection can be used successfully on nonporous and fairly smooth mate rials such as metals, glass, plastics and fired ceramics.
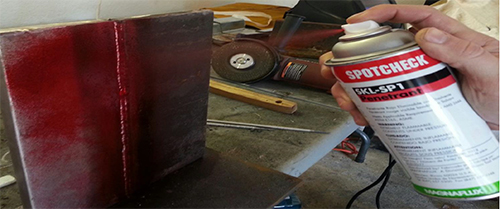
Positive Material Identification (PMI) is a NDT means of determining the chemical composition of metals. In a global sourcing environment, material can inadvertently be mixed up and cause serious issues while in service.
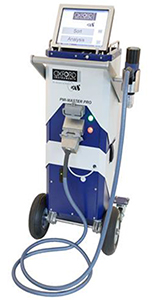